What is mixed convection laminar flow heat transfer?
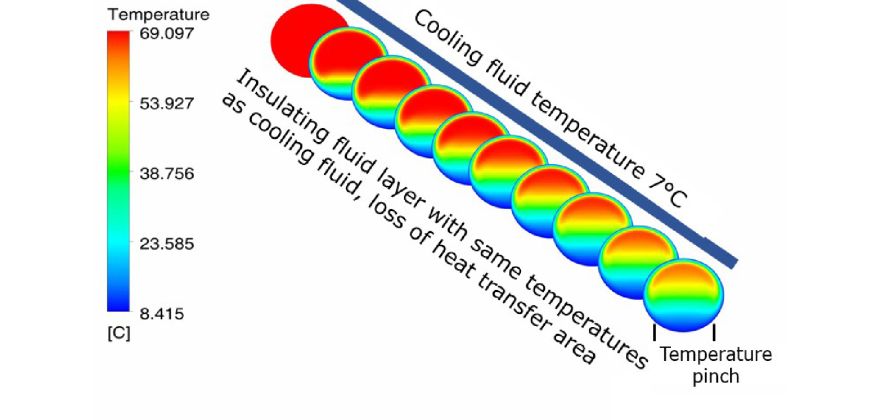
A common thermal design misconception is that laminar flow heat transfer is simple to predict and correlate in comparison to heat transfer in turbulent flow. Although laminar flow in forced convection heat transfer can be effectively modelled, design engineers often disregard the hydrodynamic and thermal effects of natural convection.
For most industrial heat exchanger cases operating in laminar flow, natural convection effects in conjunction with forced convection must be considered, otherwise known as mixed convection heat transfer.
The graph below shows measured tube side heat transfer (CALGAVIN test facility) for water at different temperatures differences between water inlet and wall temperature. It can be seen that in turbulent flow after applying a wall correction factor, all measured values line up using a Dittus-Boelter type equation.
However, it is notable that in laminar flow, the tube side heat transfer is dramatically affected by the temperature difference between bulk flow and tube wall. Larger temperature differences cause larger natural convection effects.
What can we take away from these measurements?
· In industrial relevant applications usually there are no natural convection effects in turbulent flow, therefore Nu ~ f(Re; Pr) type equations sufficient to calculate the tube side heat transfer
· Onset and extent of transitional flow region depends on natural convection effects
· Laminar flow heat transfer can be very much affected by natural convection effects, therefore Nusselt correlation becomes much more complex (Nu ~ f(Re; Pr; Ri; d/L). This leads to much larger uncertainties, when designing for such conditions.
CFD is a powerful tool to explain laminar flow forced and mixed convection in detail. To demonstrate this, we simulated a case which we experimentally verified at our CALGAVIN heat transfer test facility. This is shown in the video below. The viscous heat transfer fluid enters the 1’’ tube with a temperature of 70°C. It is cooled on the outside with cooling water of 7°C. (blue colour). On the left-hand side, just the forced convection behaviour is shown, this means natural convection effects are excluded (indicated with crossed g). When traveling with the fluid it is notable how the fluid is cooled concentrically toward the centre of the tube. For this forced convection behaviour analytically derived heat transfer solutions are available.
As explained before, in industrial exchanger design natural convection effects have to be taken into account, and the flow pattern can become much more complex, as shown in the right-hand side of the video
When flowing through the tube the liquid is cooled at the tube wall, the density increases and therefore the liquid moves downwards and displaces the less dense hotter fluid at the bottom of the tube. The displaced hotter fluid travels in the centre of the tube towards the top. As a result, the flow can become heavily temperature stratified. In extreme cases this leads to a so called in-tube temperature pinch, where there is a loss of driving temperature difference, and the bottom fluid forms an insulating layer.
It is inherently difficult to correlate mixed convection flow heat transfer accurately and uncertainties up to 50% with respect to the calculated heat transfer are not uncommon. Eliminating these uncertainties can be achieved by utilising inserts like hiTRAN, which have been extensively tested experimentally under these conditions.
If you want to learn more about those conditions and how to:
· Improve heat transfer up to 8 times without pressure drop penalty in heat exchanger design
· Avoid temperature stratification
· Warrant heat transfer performance
Sign up to our knowledge base portal (1) (https://calgavin.com/resource-portal) and access dedicated webinars around single phase flow & hiTRAN enhanced heat transfer:
Principles of Single-Phase Heat Transfer in Round Tubes | Resource Portal
hiTRAN Heat Transfer Enhancement in Single Phase Flow | Resource Portal
(1) Sign up for portal only for interested parties with verifiable company email address