Offshore
- Reducing
- - Weight
- - Space
- - Capital cost
Oil Refining
- Increased
- - Throughput
- - Energy efficiency
- - Operability
Petrochemicals
/ Chemicals
- Improved
- - Profits
- - Mass transfer
- - Product quality
Gas
- Mitigating
- - Capital costs
- - Operating costs
- - Underperformance
Power
- Greater
- - Performance
- - Optimisation
- - Profits
Enhancing exchangers across all industry sectors
Globally CALGAVIN® has brought process benefits to a variety of plants reducing capital and operating costs through increased performance efficiency within most, if not all, industries.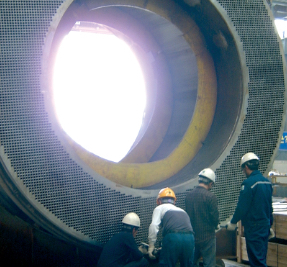
SINOPEC
China, EOG CondenserEO Plant
Provided increased heat and mass transfer allowing manufacture of exchanger within column size constraints. Kept tube count to a minimum for 4 units of 7000, 9000, 15300 & 14100 tube bundles.
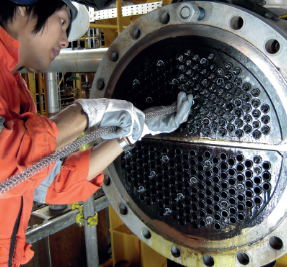
PTT
Thailand, Lean/Rich TEG ExchangersFPSO
Enhancement provides 92% increase in tube side coefficient resulting in 30% increase in overall duty. Successfully de-bottlenecked the existing unit.
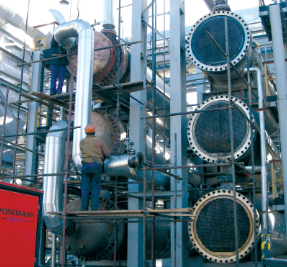
LUKOIL
Russia, Feed Effluent ExchangersHeavy Naphtha Unit
Furnace capacity limited production. hiTRAN® enhancement adds 4.6MW extra heat recovery. Very short payback.
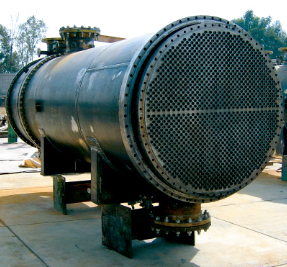
PEMEX
Mexico, Dry/Wet Crude ExchangersOffshore Terminal
Increased heat transfer results in a reduction of shells from 20 to 8. Plot space reduced by 76% and capital costs savings over US$2M.
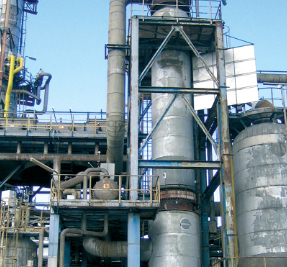
BP Germany
Feed Effluent Exchangerp-Xylol Unit
Enhancement provides 15% increased throughput from adding 0.8MW more heat recovery. CO2 reduced by 1700 t/y.

ESSO
Australia, Condensate HeatersGas Plant
With an increase in throughput, this brought about film boiling which was mitigated using hiTRAN® and still achieved required outlet temperatures at the increased duty.
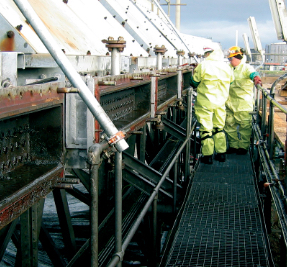
ESSAR OIL
UK, Diesel Rundown CoolersOil Refinery
hiTRAN® Thermal Systems were used for a new design to operate with 2-3 deg Celsius temperature difference between the ambient air and diesel gas oil terminal temperatures, for both summer and winter conditions,keeping within plot space constraints
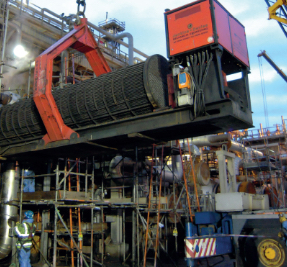
VALERO
UK, Crude Oil Preheat ExchangerVacuum Distillation Unit
Retrofit increased wall shear stress from 0.7 to 2.1Pa and increased the overall heat transfer by 262%, enabling 12 Degree Celsius lower average wall temperatures mitigating fouling and increasing run time.
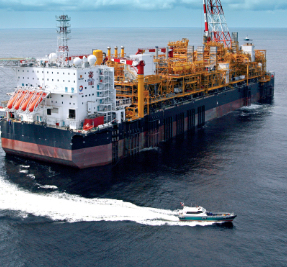
TotalEnergies
Angola, Wet/Dry Crude ExchangersFPSO
500% increase in co-efficient reduces shells from 9 to 2. Weight reduced from 401 tonnes to 130 tonnes. Cost reduced to 65%
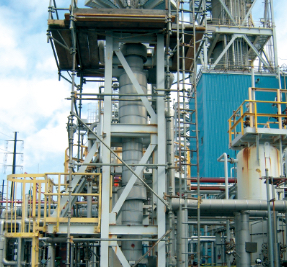
BRASKEM
USA, Vent CondenserPolypropylene plant
Significantly exceeded performance expectation. Saved capital cost of exchanger replacement. 13% increased product retention.
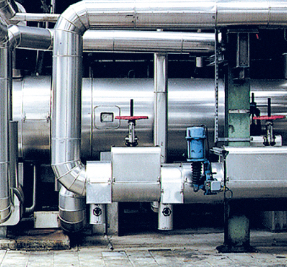
BP
Germany, Gas Oil/Crude CoolerVacuum Distillation
Unit Process fluid flow viscosity of up to 400cP was enhanced on both the tube side and shell side reducing capital cost of a new design by $128,000 for one unit, with 52% reduction in heat transfer area.
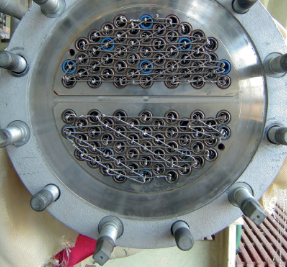
NEXEN PETROLEUM
UK, Lean/Rich Glycol ExchangerGas dehydration package, Offshore Platform
Enhancement in Duplex material was provided in order to meet a specific duty but keep within plot space constraints for the platform. With a standard design this was not possible, only achievable with tube side enhancement.
Why choose CALGAVIN?
Credibility
CALGAVIN has grown its engineering expertise for over 40 years, working with many global energy companies, EPC contractors and equipment fabricators.
Trusted Partner
We understand our clients’ challenges, listen to their needs and expectations, ensuring project success.
Case Studies
Improvement to plant needs to be the least risk, cost-effective and using proven technology. Case studies prove why we are confident.
Fundamental Research
Understanding the fundamentals of heat and mass transfer and their application to industry underpins our investment in research to support our innovation and process solutions.