Harnessing the power of CFD
CFD is a computer model of fluid flow that uses a program to solve the Navier-Stokes equations. This is done by using CAD to draw the geometry from which a mesh of the fluid volume is produced. The mesh is made up of many thousands or even millions of individual elements.
For each element, the program solves the Navier-Stokes equations based on the information for adjacent elements. The program iterates through this process until it converges on a result. CFD can also be used to investigate complex fluid flows inside tube using non-Newtonian fluids or high viscosity fluids.
A considerable amount of information can be obtained from the results, and this includes velocity and temperature profiles to vector plots and more detailed numerical results. This is ideal for example when investigating a heat exchanger geometry for areas of high velocity that may cause vibrations or areas of maldistribution.
CALGAVIN® uses ANSYS CFX® and ANSYS Fluent®.
Introduction to Computational Fluid Dynamics
Did you know CALGAVIN® offers CFD services?
This enables us to gain a comprehensive understanding of fluid behaviour in the Heat Exchanger, allowing us to identify problem areas in relation to heat transfer and fluid flow.
16% underperformance root cause identified
The Challenge
An existing Lube oil cooler in the field was reported to be under performing by 16% lower than the expected duty and 50% less pressure drop than the design. A possible cause of this was a bypass of the tube, with broken or missing weld and vent hole in the pass partition plate being the most likely areas of bypass. An endoscope was used to look inside the header but revealed nothing abnormal.
What we did
CFD simulations were set up for the tube side geometry of the lube oil cooler. The simulations investigated different vent hole diameters and missing and broken welds. These cases were compared to a simulation with no bypass.
The Result
The CFD simulations revealed that the larger the vent hole in the pass partition plate the more the duty was reduced by the bypass. However, a vent hole of the size specified on the lube oil drawing was not enough on its own to take into account the under performance.
The CFD simulations also showed with missing welds, the calculations were similar to the performance reduction reported. Therefore, it was concluded there were missing or broken welds in the header. An investigation with a thermal imaging camera confirmed that is was the case. This showed the power of CFD helped us direct our investigations to target the route cause of the under performance.
Successful simulation achieves verification of deep laminar flow conditions
The Challenge
The customer needed increased heat transfer for a polymer heat exchanger. The polymer had viscosity of 2000cP and low Reynolds numbers down to 2. Further validation was needed to ensure hiTRAN® would perform as expected in such high viscosity and low Reynolds conditions.
What we did
CFD simulations were set up for a single tube of the heat exchanger. The simulations investigated the empty tube and hiTRAN geometry for the conditions found in the exchanger. Both simulations were compared. A wall temperature profile was used in the CFD simulations to match the results from the heat exchanger design software.
The Result
The CFD simulation results showed that hiTRAN will perform as required by the customer and that it will achieve a more even temperature profile along the tube. As a result there have now been two retrofits taken for this application showing that CFD as a tool can support proposed heat exchanger solutions.
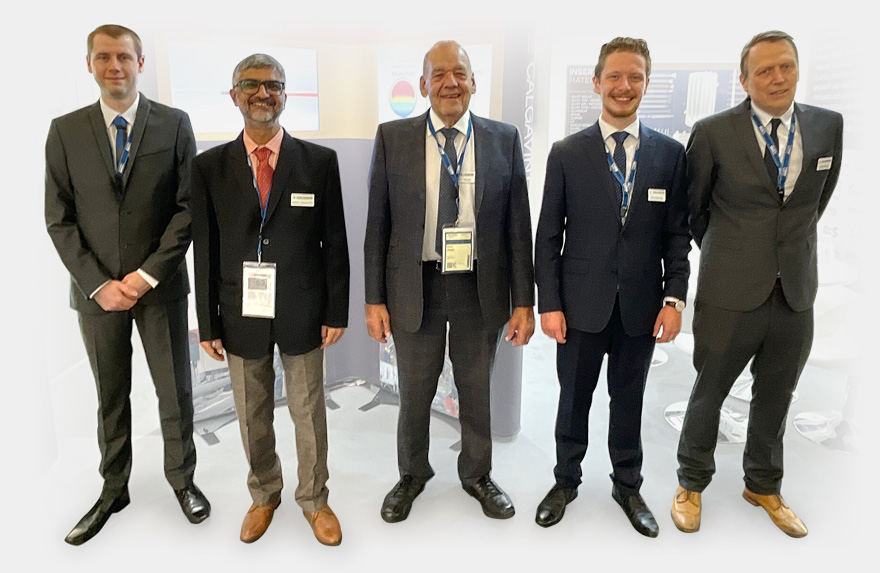