Heat Exchanger Problems - Part 1
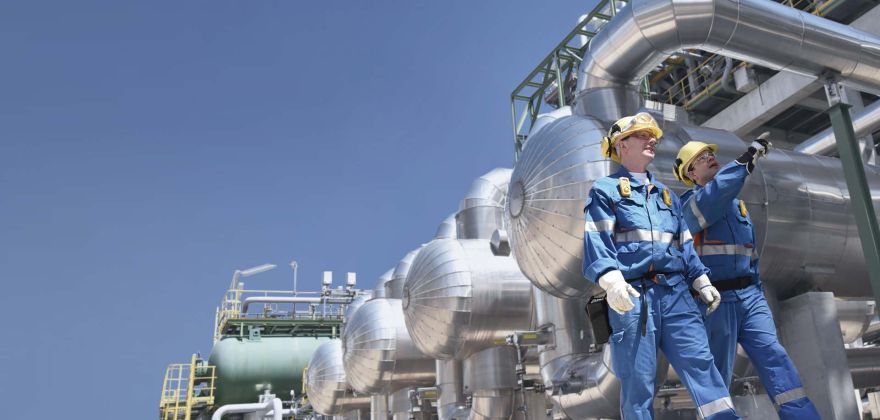
Pass Partition Bypassing
Many heat exchangers rely on pass partition plates to direct flow in multiple passes through the heat transfer surface. Shell and tube exchangers, air-cooled heat exchangers and even some compact heat exchanger types use pass partition plates to create multiple passes and therefore increase the heat transfer rate by increasing the effective fluid velocity.
Performance issues with such heat exchangers can often be traced to bypassing of pass partitions, where the fluid is able to flow around the pass division rather than through the heat transfer surface. In most cases this bypassing is the result of the failure of a gasket to provide an effective seal.
Because most heat exchanger headers need to be removable for maintenance, a bolted and gasketed joint is used to facilitate disassembly. A typical arrangement for a shell and tube heat exchanger (TEMA A type head) is shown in Figure 1.
Fig 1. typical shell and tube arrangement
There are numerous potential causes of pass partition bypassing. Some of the most common are described below.
Incorrect Gasket Position
The most straightforward cause of bypassing is the failure to position the gasket correctly during assembly – the gasket cannot provide a seal if it is not compressed in the joint. Incorrect positioning of the gasket is more likely if a flat-face joint is used, rather than the preferred confined joint. A confined joint (where the gasket fits into a machined groove) also helps to avoid the gasket being pushed out of the joint during operation.
Pass Partition Weakness
The metal plate forming the pass partition is not defined as a pressure-containing part and therefore is not subject to any mandatory rules regarding its strength. It is therefore easy to underestimate the strength required so that the plate fails under the loads experienced during operation. These loads arise primarily from the differential pressure across the plate caused by pressure losses in the heat exchanger.
For shell and tube exchangers this problem can usually be averted by following the guidance included in the TEMA Standard, and by ensuring that pass partition attachment welds are of the full penetration type. Nevertheless, application of the TEMA guidelines requires the designer to predict the highest pressure drop likely in operation and to account for the potential influence of material loss through corrosion. In practice, many pass partition failures have been caused by a pressure drop in excess of that expected. Such excess pressure drop is often the result of fouling or incidents of temporary high flow following the action of pressure relief devices.
Tubesheet / Flat Cover Deflection
In many heat exchangers, the pass partition gasket is compressed against either the tubesheet or a flat cover or both (as in Figure 1). In operation, internal pressure tends to cause deflection of these components with the consequence that the gasket is relaxed and leakage occurs. Such deflection might be expected when the operating pressure is high, but the problem is most frequently experienced with large exchangers operating at relatively low pressures. In such cases, the tubesheet and/or cover may be relatively flexible while meeting pressure vessel code requirements.
Bypassing related by this effect may be difficult to diagnose because the problem only occurs during operation. When shut down for inspection the components return to their flat profile, giving no indication of the cause of the problem.
Tubesheet and/or flat cover deflection can be prevented by ensuring adequate stiffness in these components over and above the requirements of the pressure vessel code. Again, TEMA provides some guidance in the case of shell and tube heat exchangers. Alternatively, an internal pass partition box can be used with a TEMA C type head (See Figure 2) where the pass partition gasket is compressed independently of the tubesheet or flat cover.
Fig 2. TEMA type C Shell & Tube Exchanger
Pass partition bypassing is a common cause of heat exchanger performance problems. If poor performance is experienced in conjunction with lower-than-expected pressure drop it should figure as the most likely culprit. Confirmation of the problem can be problematic, however. Physical evidence (such as displaced gaskets or erosion of partition gasket seating faces) may not be apparent, or the operator may wish to avoid a shutdown to inspect without supporting evidence. In such cases, the use of infra-red imaging or residence time analysis (tracer injection) may provide insights while the equipment is still online.
Once pass partition bypassing problems have been correctly identified, an appropriate solution can be engineered and applied.
Linked Articles
- Heat Exchangers - Part 2 - High Flux Vaporisers
- Heat Exchangers - Part 3 - Hot Air Recirculation in Air Cooled Heat Exchangers