Energy Reduction Strategies for Catalytic Reactors – Part2
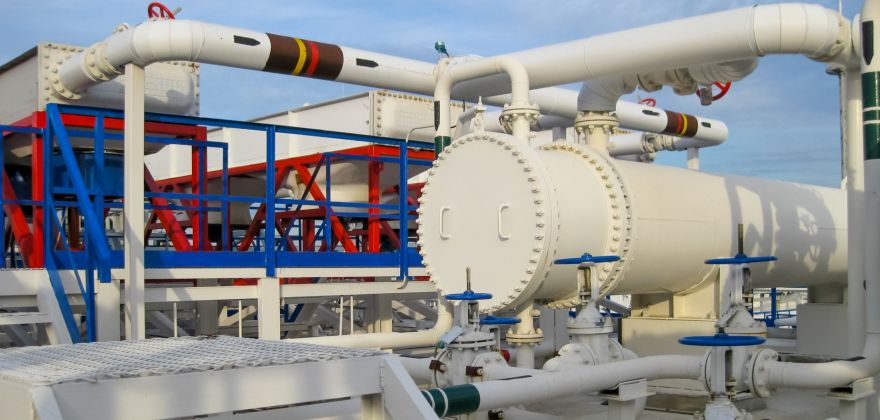
Design choices of Feed/Effluent Exchangers
There are four main choices of heat exchanger design that lend themselves to feed/effluent services which are driven by the factors explained in part 1 of this article. Each individual design will follow the ideal temperature cross needed for efficient heat transfer. The design choices are as follows:
- Texas Tower
- TEMA ‘F’ Type
- TEMA ‘E’ Type with shells in series
- Packinox
Each design choice has its own advantages and disadvantages which are summarised below.
Generally, the advantages for all of these design choices are a combination of the following; counter current flow for efficient heat transfer, low pressure drop, less phase separation, floating heads of exchangers enabling easy maintenance, low CAPEX costs, straight forward mechanical design and compact designs.
The disadvantages to these designs can be difficulties in cleaning when fouling does occur, bellows failing creating internal leakage for some designs, high pressure drops, maldistribution, high CAPEX costs and sensitivity to heat release curves.
Overall no matter what design is chosen there will be disadvantages where novel retrofit technologies can be used to increase the heat recovery of a feed/effluent exchanger and as an alternative to a replacement heat exchanger.
Heat Transfer Enhancement Technologies
There are technologies available on the market that can be applied to both sides of a feed/effluent exchanger. For the shell side as an alternative to the standard segmental baffle, you have the options of EM Baffles or Helical Baffles. Each type of baffle creates the enhancement needed in two different ways.
EM Baffles improves the heat transfer longitudinal along the tube creating turbulence around the tubes with every EM Baffle the fluid meets. An ideal application for this type of Baffle is where you need to reduce the shell side pressure drop but still maintain or increase the heat transfer. TEMA ‘F’ Type exchangers are a good example where shell side pressure drop can be an issue and an alternative to the standard baffle design would be an advantage.
Helical Baffles work on the principle of creating a helical flow on the shell side around the tube bundle, thus creating turbulence on the outside of the tubes improving the heat transfer. An example of where helical baffle can be applied is in the vertical orientation for Texas Towers.
For tube side enhancement there are technologies such as twisted tape and also CALGAVIN®’s proprietary hiTRAN® thermal systems. Twisted tapes work by inducing a swirl flow velocity which in turn creates shear at the tube wall creating turbulence, in this application there needs to be a sufficient velocity in order for the swirl flow to be created.
hiTRAN thermal systems work by disrupting the laminar boundary layer at the tube wall changing the mode of heat transfer from conduction to convection, which in turn is a faster rate of heat transfer. In addition, the bulk flow is also directed and mixed with the fluid at the tube wall creating turbulence which is important for efficient heat transfer.
Each type of technology has shown to be effective in compensating and recovering energy in instances where disadvantages in designs are a problem.
Case Study
CALGAVIN has proven case studies’ promoting the use of hiTRAN thermal systems in instances where there is an opportunity to save energy and costs through increasing heat transfer for critical heat exchangers.
In summary, there is one case study that shows the benefits of heat recovery for feed/effluent exchangers.
For a Texas tower type design for Ruhr Oel in Gelsenkirken, Germany a feed/effluent exchanger was in operation for 30 years and a proposed 17.5% increase in throughput was planned. However, the fired heater was at full load and the catalyst for the Paraxylene reactor had degraded; so much so that the maximum inlet temperature entering the reactor had been reached.
There were 3 options available to the client:
- Replace the fired heater with a larger heater incurring high CAPEX costs and burning more fuel.
- Replace the Texas tower with a larger unit incurring high CAPEX costs and changes to re-pipework.
- Improve the performance of the existing Texas tower and see the effect on the process.
Option 3 was looked at and a decision was made to install hiTRAN into the exchanger. This decision avoided replacing plant equipment and reduced catalyst renewal requirements which removed potentially high CAPEX costs.
CALGAVIN engineers also identified poor flow distribution on the tube side, mist flow in the process stream and wall dry out occurring through film boiling.
By analysing the heat transfer improvement with hiTRAN and the pressure drop implications, a hiTRAN type was designed and installed to give the following benefits.
- The effect of poor flow distribution, mist flow and film boiling was mitigated.
- In the boiling region, the tube side heat transfer coefficient increased by 11%.
- In the super-heated region, the overall heat transfer coefficient increased by 48%.
- With the increased heat recovery of the exchanger, the existing fired heater duty capacity was within the proposed new throughput.
- With a reduction of 0.8MW in duty, this equated to 1700te/yr reduction in CO2 output.
- The hiTRAN was installed in the normal shutdown period.
- The payback period for the installation was within 18 months.
Overall an Excellent Return on Investment!
In conclusion, there is no perfect design for a feed/effluent exchanger. Where there are deficiencies in any design the first task is to identify them and then if necessary investigate retrofit technologies that can possibly improve upon these. Technologies such as hiTRAN offer the improvement in heat recovery and yield but still reducing the amount of energy needed for required duties.
Product quality is increased with no significant changes made to the plant achieved within a small payback period compared to alternative solutions.
With industry pressures to increase throughput but reduce energy consumption put upon plant operators, technologies such as hiTRAN are a firm solution!
Linked Article
- Energy Reduction Strategies for Catalytic Reactors – Part 1 - Catalytic Reaction Processes