Case Study: Polypropylene Plant Revamp
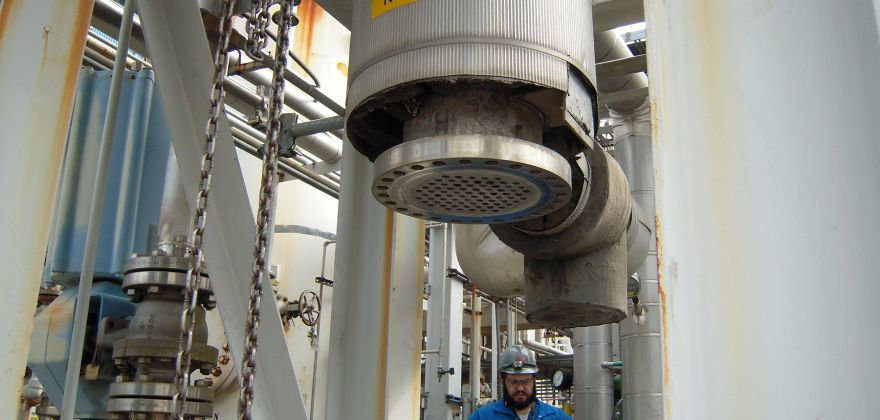
CALGAVIN® were chosen to perform a technical evaluation for a Polypropylene interchanger at a Polymers Plant in the USA.
The Problem
The exchanger was in the service of refrigeration, utilizing liquid polypropylene as the refrigerant. The interchanger was part of a crucial recycling operation where it was desired to recover polypropylene from a waste stream.
The interchanger was underperforming, producing an outlet temperature greater than 50°F(10°C). During the summer conditions, ambient air temperatures were running over 90°F (32°C) increasing the cooling water temperatures, resulting in unwanted gas exiting the aftercoolers and entering the interchanger.
Tank levels of unrecovered Propylene in the refrigeration, equated to greater than 25%, of which some of the product was lost in the flare header.
The Objective
The project objective was to increase the performance of the interchanger and reduce the residue of the waste stream going to the flare header by 10%, with minimal disruption to the production schedule, and with no major alterations to the plant equipment.
The solution was to Install hiTRAN® Thermal Systems into the bottom section of the exchanger, vertically upwards from ground level.
The Solution
This was a particularly challenging installation where it was necessary to demonstrate the adaptability of the CALGAVIN engineers and installation staff, as well as willingness to provide the best solution under difficult circumstances and time constraints.
Bottom of Interchanger with hiTRAN fitted
Further analysis of the exchanger by CALGAVIN had established that the main section of the interchanger, where the most significant activity took place, was the bottom third.
After the installation of hiTRAN elements, the interchanger performance was greatly improved. The outlet temperatures now averaged -10°F (-23°C) and propylene levels unrecovered had now dropped by 18%. This meant the levels of propylene that reached the flare header in the waste stream after the installation had reduced to just 2-3%, compared to 15% prior to hiTRAN revamp.
Economic evaluations carried out by site engineers concluded that the propylene savings made from this installation had a pay-back period for the project of less than one month.
Benefits
- “Quicker delivery time of the interchanger” – a higher rate of production as a result
- “Cheaper purchase cost of similar interchangers” – considerations such as less metalwork required, size and space benefits also
- “Ease of installation” – leading to minimal downtime, saving considerable cost
- An increase of 10-13% of product retained that would have otherwise been burnt in a flare header.
Client Testimonial
The Chief Process Engineering Specialist on site was very happy with the improvements gained after installing hiTRAN.
“I still cannot believe the change. The before and after performance, of the interchanger, was even better than expected. We achieved all the savings that we projected in the project economics, plus a lot more. We have been very happy with your product; it gave us the operating performance that we desired without having to replace the interchanger with a completely new heat exchanger. ”
“Possibly the best money I have ever spent in a 37 year engineering career.”